President Donald Trump has officially imposed a 25% tariff on imported passenger vehicles, light trucks, and select auto parts as of April 2025. While the United States-Mexico-Canada Agreement (USMCA) provides temporary exemptions for some vehicles that meet specific criteria, many foreign-made components within those cars remain subject to the tariff.
This move is expected to drive up vehicle prices and could lead to a significant drop in U.S. automotive production—potentially by as much as 30%—causing widespread disruptions across the supply chain.
Millions of jobs in manufacturing and retail may be at risk, and the U.S. auto industry could lose competitiveness on the global stage.
Amid this uncertainty, Additive Manufacturing (AM) is emerging as a crucial tool. By enabling faster, localized, and more flexible production, AM is helping manufacturers adapt to shifting supply chains and reduce reliance on foreign-sourced parts.
The Tariff Ripple Effect: A Snapshot
The new tariffs don’t just affect imported vehicles. Even domestically assembled cars rely on imported parts—from engines and transmissions to essential electronics—which will now face added costs.
The Fallout Could Include:
-
Higher consumer prices, both at the dealership and through reduced incentives (e.g., higher loan interest rates).
-
Production slowdowns, with up to 20,000 fewer vehicles rolling off assembly lines each week.
-
Job losses, potentially impacting up to 3 million workers across factories and showrooms.
-
Strategic pullback, as global automakers reconsider investments in a now costlier U.S. market.
Additive Manufacturing: A Strategic Response & Case Study
Additive Manufacturing, also known as 3D printing, is emerging as a powerful tool to offset the impact of trade restrictions. Its ability to localize, simplify, and accelerate production makes it a perfect fit for an industry facing disrupted supply chains and cost pressure.
1. Localized Supply Chains – Using 3D Printing to cut fixture setup time by 97%
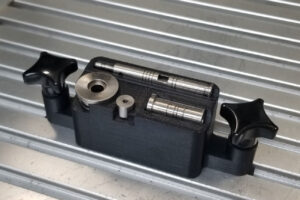
When Christopher Tool, a family-owned manufacturer, faced time-consuming and inconsistent setups for laser-marking a wide variety of precision parts, they turned to additive manufacturing for a solution. By bringing 3D printing in-house, they began producing custom ABS fixtures tailored to each part—right on-site. This shift didn’t just streamline their process, slashing setup time by an incredible 97%, it also eliminated reliance on outsourced or machined jigs. The result? A faster, more flexible operation that localized their supply chain and ensured consistent, high-quality results—all from the factory floor. It’s a powerful example of how additive manufacturing empowers businesses to respond instantly, locally, and with precision.
2. Reduced Cost & Lead Times
3D printing with FDM Nylon 12CF allowed General Motors to produce conveyor risers that were 32% lighter than aluminum and 72% lighter than steel. This switch eliminated the need for special welding and offsite maintenance. As a result, production lead time was reduced from nine weeks to just two, achieving a 75–80% time savings. Additionally, costs were lowered by minimizing post-machining and maintenance requirements, demonstrating how additive manufacturing can streamline production and enhance efficiency.
3. Production Agility
Additive tech allows fast iteration, repair, and adaptation—critical during uncertainty. Continental enhanced its production agility by integrating the Fortus 450mc 3D printer at its ADaM Competence Center. This enabled rapid, on-demand manufacturing of replacement tools and production parts using high-performance thermoplastics like ULTEM 9085 and ABS-ESD7. Parts can be printed overnight, reducing downtime and eliminating delays from traditional manufacturing. The system allows quick, ESD-compliant customization, especially valuable for electronic components, ensuring safe, efficient production while responding flexibly to evolving manufacturing needs and customer demands.
4. Customization & Design Freedom
As supply chains tighten, AM enables manufacturers to innovate and differentiate without retooling entire production lines. 3D printing with the Stratasys Origin One gave NISMO Racing expanded design freedom by enabling the creation of highly customized, end-use parts with advanced materials like Loctite IND 402. Engineers rapidly iterated yoke handles and button gaskets, achieving ideal comfort, durability, and a rubber-like feel tailored to driver feedback. Freed from tooling limitations, NISMO dramatically accelerated development—compressing months into days—while exploring innovative solutions for performance-critical components, ultimately enhancing their competitive edge in the fast-paced world of motorsport engineering.
The Road Forward
While additive manufacturing may not yet replace high-volume vehicle production, it’s proving invaluable for rapid prototyping, tooling, low-volume components, and supply chain resilience. As the industry braces for tariffs and transformation, AM is no longer a luxury—it’s a necessity.
The automakers who embrace it today will be the ones still leading tomorrow.